Key Components of Quantity Sheets in Construction Projects
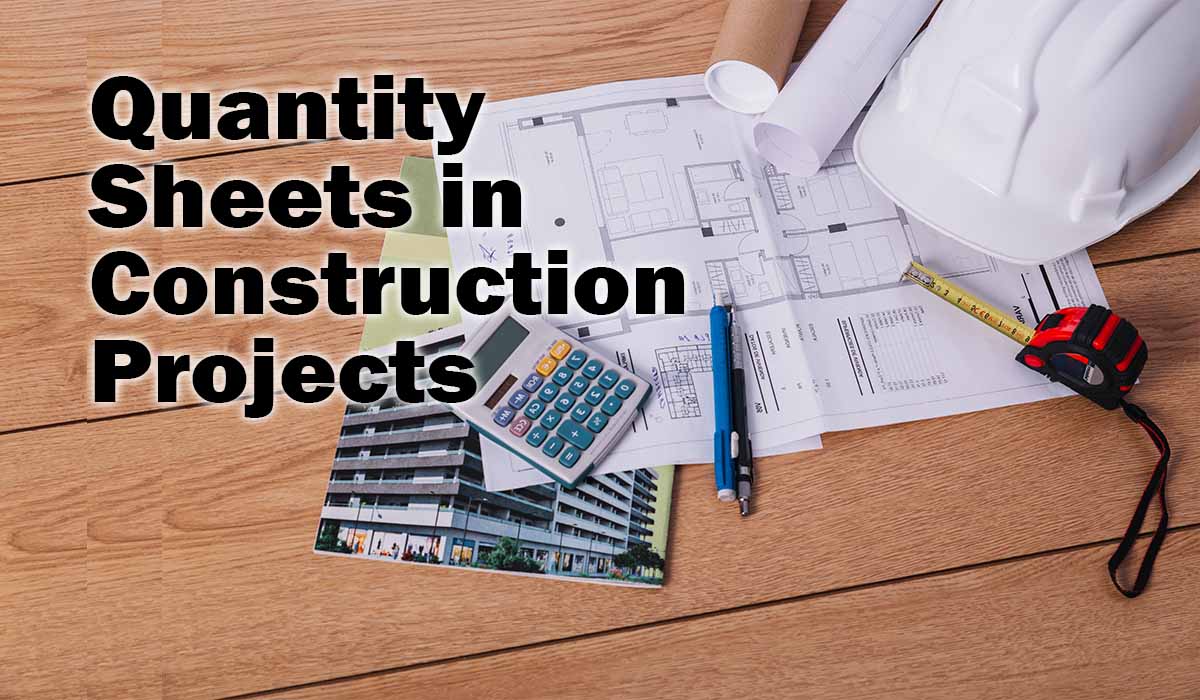
In construction, precise planning is critical to success. One of the most crucial tools used to ensure project efficiency is the quantity sheet. In this blog post, we will explore the key components of quantity sheets in construction projects, how they are used, and provide a guide to creating them accurately. Whether you’re a contractor or a project manager, understanding these sheets can significantly improve project management and cost estimation.
What Are Quantity Sheets and How Are They Used?
Quantity sheets, also known as bill of quantities (BOQ), play a pivotal role in construction project planning. These sheets list materials, labor, and other resources required for a project. They are essential for budgeting, purchasing, and organizing the timeline of a construction project.
Why are they important?
- Cost Estimation– Quantity sheets help estimate the total project cost, including materials and labor. By laying everything out in detail, project managers can avoid surprises and ensure everything stays within budget.
- Resource Management – Quantity sheets also streamline resource management. They provide a comprehensive view of the materials needed and when, allowing for efficient scheduling and procurement.
- Project Monitoring – Quantity sheets are often used as reference documents during project execution, helping teams monitor the progress against planned resources and costs.
If you’re managing construction projects and need professional assistance with quantity and estimation services, feel free to visit our building plan and quantity estimation services for expert help.
Key Components of Quantity Sheets in Construction Projects
Now that you understand what quantity sheets are, let’s delve into the key components of quantity sheets in construction projects.
1. Item Description
Each quantity sheet begins with detailed descriptions of every material or service required for the project. This includes specific product types, sizes, and specifications.
2. Unit of Measurement
Each item must be assigned a unit of measurement, whether it’s in cubic meters, square feet, or kilograms. This ensures consistency and clarity in procurement.
3. Quantity
For every item listed, the exact quantity required is noted. This helps avoid wastage and ensures that the right amount of materials is available at every stage of the project.
4. Rate
This refers to the cost per unit of each material or service. Rates vary based on suppliers and market conditions, making it important to update these regularly.
5. Amount
Once the quantity and rate are set, the total amount for each item is calculated. This gives a clear picture of how much each part of the project will cost, making it easier to manage the overall budget.
6. Remarks or Notes
Any special instructions or comments related to materials, suppliers, or timing are added in this section. It ensures everyone involved has the necessary details for smooth project execution.
Understanding these components is vital in creating accurate and functional quantity sheets. If you are involved in any large-scale project and require help managing your quantity sheets, we can provide detailed quantity estimation services to ensure success.
Step-by-Step Guide to Creating Accurate Quantity Sheets
Creating a quantity sheet can seem daunting at first, but following a structured process ensures accuracy. Here’s a step-by-step guide:
- Review the Project Drawings – Before drafting the sheet, thoroughly review the architectural and engineering drawings. This helps you determine what materials and labor are necessary.
- List All Required Materials – Based on the drawings, list every material, service, and labor required for the project. Be as specific as possible to avoid ambiguity later.
- Assign Units of Measurement – For each material or service, assign the proper unit of measurement. This step is critical for procurement and keeping the project on track.
- Determine Quantities – Calculate the precise quantity of each item. Accurate measurement is key, as underestimating can delay the project, and overestimating may lead to waste.
- Calculate Costs – Research the current rates of materials and services and multiply by the quantities required to arrive at the total cost.
- Double-Check and Verify – Go through the sheet to ensure everything is accurate and nothing has been left out. It’s wise to have a second set of eyes review it for errors.
By following these steps, you can create precise and detailed quantity sheets that contribute to the successful completion of construction projects.
Conclusion
Understanding the key components of quantity sheets in construction projects is essential for project managers and contractors alike. By mastering these tools, you can ensure your projects stay on time and within budget, avoiding costly errors. Whether you’re new to construction management or looking to refine your skills, accurate quantity sheets are an invaluable resource.
If you’re looking for top-quality building plans and quantity estimation services, check out our www.planesti.com for expert solutions. Additionally, for convenient daily use products, explore our external online shop, offering a wide range of products to simplify your life.
FAQs
Quantity sheets are used to list materials, labor, and services required for construction projects. They help with budgeting, procurement, and project management.
Accurate quantity sheets are calculated by reviewing project drawings, listing materials, assigning units of measurement, determining quantities, and multiplying by the cost rate of each material.
Yes, quantity sheets help reduce costs by providing an organized way to plan materials and avoid wastage, ensuring efficient use of resources.
Common mistakes include miscalculations, incorrect measurements, and failing to update rates based on current market prices.
Yes, there are various software tools that can help automate the creation of quantity sheets, ensuring consistency and accuracy.
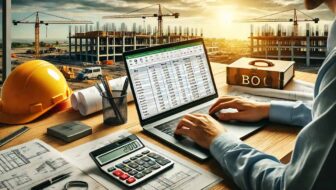
Top 10 Excel Templates for Civil Engineers: Streamline BOQs and Cost Estimation
Did you know that 63% of civil engineers waste over 5 hours weekly on repetitive tasks like manual BOQ preparation...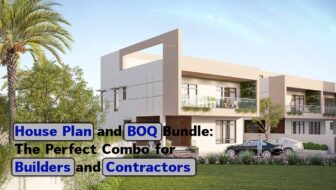
House Plan and BOQ Bundle: The Perfect Combo for Builders and Contractors
When it comes to residential construction projects, two critical elements ensure smooth execution and cost-effective results: a well-designed house plan...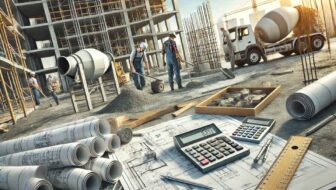