Common Mistakes to Avoid in Quantity Sheets
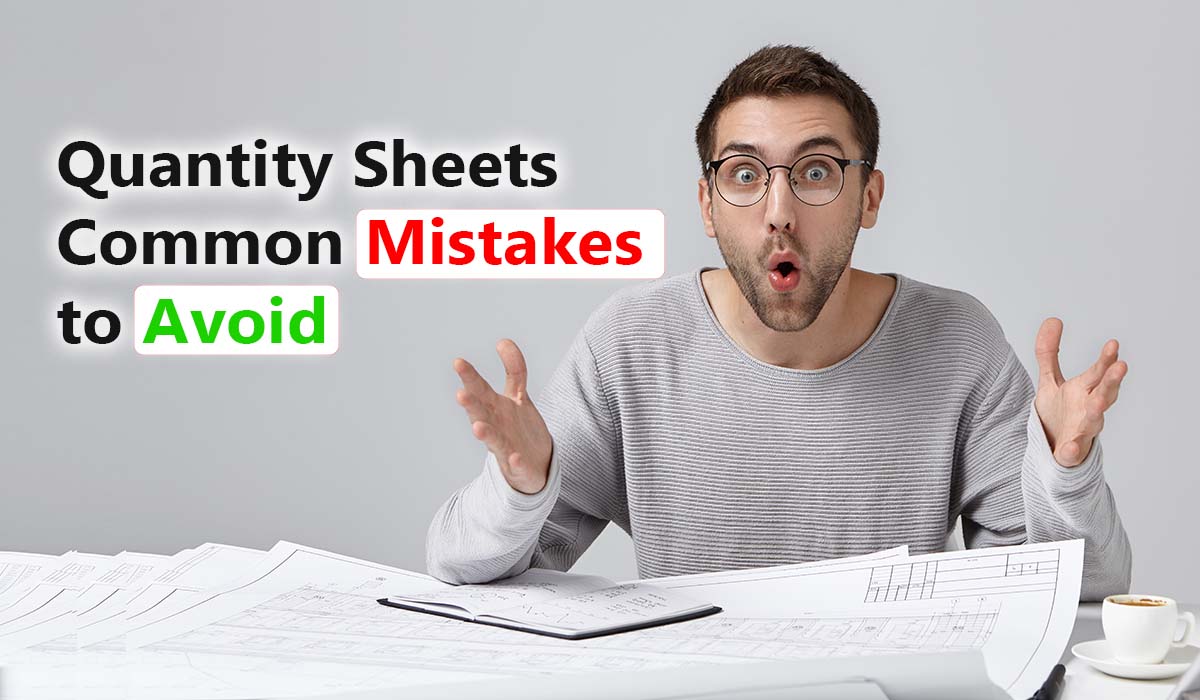
In construction and project management, quantity sheets play a critical role in ensuring projects stay on track, on budget, and meet design requirements. A well-prepared quantity sheet provides accurate data for material estimates and labor, helping to streamline the project workflow. However, even seasoned professionals can make errors when drafting these sheets, leading to costly overruns, delays, or structural issues. In this post, we’ll explore the common mistakes to avoid in quantity sheets, and how to improve your approach to enhance accuracy and efficiency.
What is a Quantity Sheet?
A quantity sheet is a detailed document that lists the materials, quantities, and types required to complete a construction project. It also includes labor and cost estimates, playing a vital role in project planning, budgeting, and execution.
Key Mistakes in Quantity Sheets and How to Avoid Them
1. Incorrect Measurement Units
One of the most common quantity sheet mistakes is using inconsistent or incorrect measurement units. This can result in inaccurate material ordering, causing delays and wastage. To avoid this, ensure that all measurements are standardized and cross-checked before finalizing the sheet.
2. Failure to Update Quantities Based on Design Changes
Design alterations are common during construction. Failing to adjust the quantity sheet to reflect these changes leads to material shortages or surpluses. Regularly reviewing and updating the sheet will help avoid such issues.
3. Misidentifying Material Types
Choosing the wrong materials can compromise project integrity and inflate costs. Each material should be carefully matched with its specific requirements in the design. Misidentifying materials can be avoided by collaborating closely with suppliers and designers to ensure accuracy.
4. Overlooking Small Items
Nuts, bolts, and other minor materials are easy to overlook, but they can affect your budget significantly if forgotten. Ensure every small item is accounted for in your quantity sheets to avoid last-minute purchasing delays.
5. Inconsistent Cost Estimations
Estimation errors in quantity sheets often occur when market prices fluctuate. Not factoring in current market trends can result in budget overshooting. Be sure to use the latest pricing data and adjust estimates accordingly.
6. Miscommunication Between Teams
When different teams (e.g., architects, engineers, and procurement) aren’t on the same page, errors in the quantity sheet can occur. To avoid miscommunication, establish clear channels for feedback and information sharing.
How to Improve Accuracy in Quantity Sheets
1. Use Quantity Surveying Software
Technology is your friend when it comes to managing quantity sheets. Modern tools allow you to automate calculations and ensure accuracy in your measurements and cost estimations.
2. Implement a Review System
Having multiple eyes on the quantity sheet can significantly reduce the chances of errors. A dedicated review system with input from engineers, procurement officers, and other stakeholders helps catch mistakes early.
3. Keep an Updated Reference Library
Maintain a well-organized reference library of material specifications, cost data, and previous projects. This can help improve the accuracy of your quantity sheets and avoid repetitive mistakes.
4. Regular Training for Teams
Ensure your team is up to date with the latest best practices in quantity surveying. Regular training sessions can help them avoid common quantity sheet mistakes and stay informed of the latest technologies.
Related Services
If you’re looking to streamline your quantity sheets and improve your project’s efficiency, consider consulting with our professional quantity and estimation services. We offer tailored solutions to ensure your projects are completed on time and within budget.
For a different type of service entirely, visit our eCommerce website for high-quality, daily-use products delivered straight to your door.
By avoiding these quantity sheets mistakes and adopting best practices, you can ensure that your construction projects run smoothly. Accurate quantity sheets are key to keeping costs in check and maintaining project timelines, so it’s essential to give them the attention they deserve. Don’t hesitate to reach out to our expert team for help with your next project’s quantity sheet preparation.
FAQs
The most common error in quantity sheets is incorrect measurement units, which can lead to significant miscalculations in material orders.
To avoid errors, double-check all measurements, keep your data updated with design changes, and use software tools to automate calculations.
Quantity sheets are crucial because they provide a roadmap for materials, labor, and costs, helping to keep projects on track and within budget.
Popular software options for managing quantity sheets include AutoCAD, PlanSwift, and CostX. These tools offer features like real-time material tracking and cost estimation.
Your quantity sheet should be updated whenever there is a design change or when there are fluctuations in material costs or labor rates.
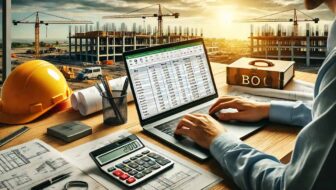
Top 10 Excel Templates for Civil Engineers: Streamline BOQs and Cost Estimation
Did you know that 63% of civil engineers waste over 5 hours weekly on repetitive tasks like manual BOQ preparation...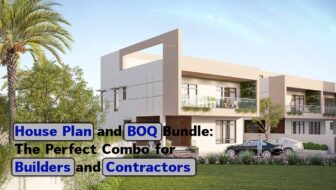
House Plan and BOQ Bundle: The Perfect Combo for Builders and Contractors
When it comes to residential construction projects, two critical elements ensure smooth execution and cost-effective results: a well-designed house plan...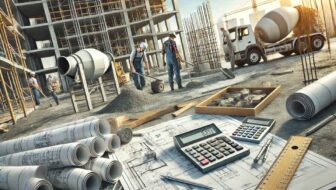